Neue vollautomatisierte Prozesslinien zur Kartoffelverarbeitung.
Die FFB-Group setzt auf die Automationslösung von ICS, um den Masterplan Kartoffel am Standort in Bischofszell zu realisieren.
ICS Automation AG
bearbeitet weltweit Automationsprojekte und ist in der Lebensmittelindustrie stark vertreten. Wir bearbeiten Prozesse von der Rohstoffannahme bis zum Fertigprodukt und implementieren dabei die nötigen Abläufe wie z.B. Rohstofftransfer, Tanklager- und Silosysteme, Dosierungen und Mischereien, etc. Vermehrt werden bei solchen Produktionsanlagen auch Einzelmaschinen oder Anlageteile integriert, welche durch uns in den Produktionsprozess eingebunden werden. Deshalb haben wir unser Knowhow betreffend Schnittstellen-Engineering Schritt für Schritt erweitert, um unseren Kunden eine lückenlose Rückverfolgbarkeit durch den gesamten Prozess zu ermöglichen.
Referenzen
Kartoffelverarbeitung
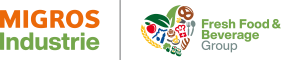
Kakaorösterei
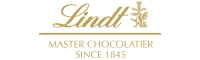
Zwei neue Produktionsanlagen für das Cocoa Center in Olten.
Lindt & Sprüngli Schweiz vertraut erneut auf das langjährige Prozess- und Automations-Know-how von ICS.
Mühlensteuerungen
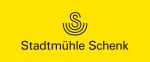
Dank der Erfahrung aus diversen Retrofitprojekten und vereintem Mitarbeiter-Knowhow durften wir einen neuen Standard für die Müllerei entwickeln und damit einen neuen Massstab in der Branche setzen. Dank verbesserter Bedien- und Überwachungsmöglichkeiten, einer effizienten Prozessgestaltung sowie branchen-spezifischer Auswertemöglichkeiten helfen wir aktiv mit, den Wettbewerbsvorteil unserer Kunden zu steigern.
Prozessoptimierung
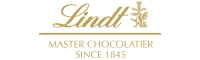
Dank dem regelmässigen Austausch mit unseren Kunden erhalten wir vermehrt Anfragen, Prozessoptimierungen mit Fokus Energieverbrauch, Nachhaltigkeit oder Minimierung von Stillstand und Ausschuss auszuarbeiten.
Integration Unterhalts-Software
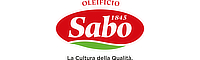
Viele unserer Kunden arbeiten täglich mit unserem Prozessleitsystem und der darin eingebetteten Prozessvisualisierung. Durch die Abbildung und Auswertung aller Steuerungselemente hat der Benutzer seine Produktionsprozesse sowie den Status der Anlagen immer im Überblick.
Steuerungsersatz Prozessanlagen
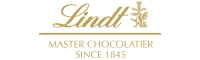
Seit bald 20 Jahren betreut die ICS Automation AG weltweit verschiedenste Produktionsstandorte für die Herstellung von Schokoladenmasse. Die ICS steuert dabei den Prozess von der Annahme der Kakaobohne bis zur Beschickung der Giessanlagen, mit welcher die Schokolade schliesslich die gewünschte Form erhält.
Speicher- und Fördersysteme
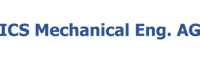
Zusammen mit unserer Schwesterfirma ICS Mechanical AG liefern wir weltweit Speicher-, Handling- und Fördersysteme für die Food- und Non-Food Industrie.
Anlagen mit Produktverfolgung
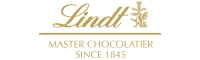
Eine der Hauptanforderung für produzierende Unternehmen ist die Rückverfolgbarkeit der Produktionsprozesse um z.B. die Lebensmittelsicherheit zu gewährleisten. Die gezielte Aufteilung des Produktionsprozesses sowie die Unterteilung in definierte Produktionsmengen (Chargen) bilden dafür das Fundament. Heutige Systeme erlauben weitere Möglichkeiten und eine beinahe lückenlose Auswertung des Produktionsablaufes.
Retrofitprojekte
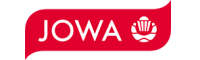
Die ICS hat in diversen Retrofitprojekten viel Erfahrung gewonnen und verfügt dank der Teamgrösse über die nötigen Ressourcen, um auch grössere Retrofitprojekte zu stemmen.
Faserzementanlagen
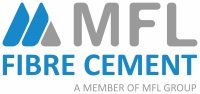
Zusammen mit der MFL Faserzement GmbH bearbeiten wir weltweit Faserzementprojekte.
Molkereien
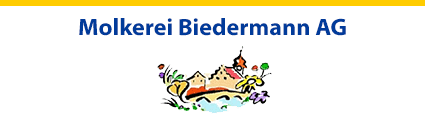
Die Molkerei Biedermann aus Bischofszell gehört zu den langjährigsten Kunden der ICS Automation AG. Dank der langjährigen Partnerschaft können die diversen Projekte effizient und ohne grosse Stillstandzeiten umgesetzt werden.
Gebäudeleitsysteme
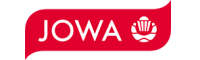
Für die Jowa in Ecublens durfte das bestehende Gebäudeleitsystem abgelöst und erneuert werden. Neben einem Steuerungsersatz der bestehenden Gebäudetechnik war vor allem die kurze Umsetzungs- und Inbetriebnahmezeit eine grosse Herausforderung für alle Projektbeteiligten.